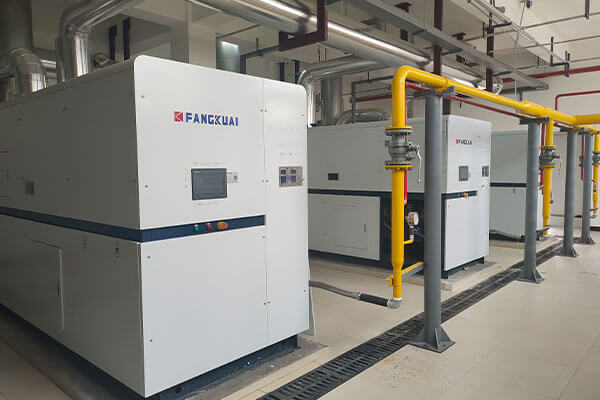
Here’s why that matters: when water vaporizes at this lower temperature, the resulting steam transfers heat more effectively through the system compared to liquid circulation. You also get reduced mineral deposits in pipes since the water doesn’t reach scaling temperatures. And unlike pressurized boilers, these systems physically can’t build up dangerous pressure levels – the vacuum seal automatically prevents overpressurization.
Basic Structure and Working Principle
A typical vacuum hot water boiler comprises two main chambers:
-
Combustion/Heating Chamber: Located at the bottom, where fuel (gas, oil, or other sources) burns to generate heat.
-
Vacuum Heat-Exchange Chamber: Sealed and evacuated to about 0.02–0.08 MPa; contains a bank of heat-exchange tubes submerged in the working fluid.
Once the vacuum pump evacuates air and dissolved gases, heating the fluid causes it to boil at the lower vacuum boiling point. The resulting low-temperature steam rises, contacts the cooler external circulating water through the tube walls, and transfers its latent heat. The steam then condenses and returns to the liquid phase, flowing back to the boiler floor to repeat the cycle—creating a closed loop that requires no makeup water and carries no explosion risk.
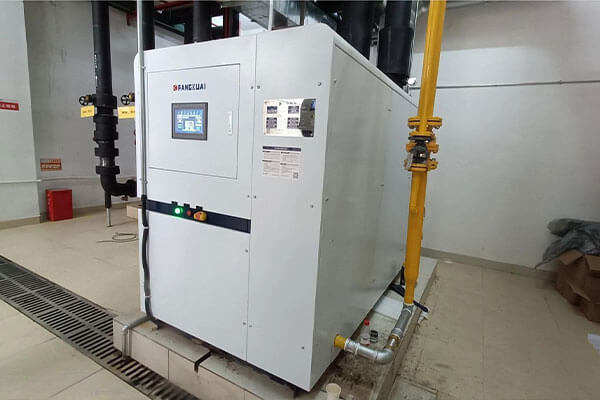
T6 Vacuum Hot Water Boiler
Phase-Change Heat Transfer Explained
At the heart of a vacuum boiler’s efficiency is the phase-change process:
-
Boiling (Vaporization): Liquid water absorbs latent heat (LvL_vLv ≈ 2260 kJ/kg) to become steam. Under vacuum, this occurs at lower temperatures (e.g., ~81 °C at 0.05 MPa), greatly reducing fuel consumption.
-
Condensation: The steam gives up the same amount of latent heat when it contacts cooler tube walls, heating the external water circuit before reverting to liquid.
Because latent-heat transfer is up to 20 times more efficient per unit mass than sensible-heat transfer, vacuum boilers can achieve thermal efficiencies above 95 % with minimal temperature differentials—and without the high flue-gas losses typical of traditional systems.
Get a quote for a vacuum hot water boiler
Vacuum Hot Water Boilers Key Advantages
-
Enhanced Safety: Internal pressure remains below atmospheric; any leak draws in air rather than emitting steam under pressure, eliminating explosion hazards.
-
Superior Efficiency: High latent-heat utilization and low flue-gas temperatures yield net efficiencies often exceeding 92 %, and in advanced designs up to 104 % (on the higher-heating-value basis).
-
Low Maintenance: Vacuum conditions virtually eliminate scale formation and corrosion, extending service life to 15–20 years with minimal downtime.
-
Compact Installation: Integrated hot-water modules save floor space and simplify piping, making rooftop or basement installations straightforward without extensive safety clearances.

T7 Vacuum Hot Water Boiler
Typical Applications
-
District and Building Heating: Precise temperature control (20–90 °C) suits radiators, under-floor heating, and air handlers.
-
Domestic Hot Water: Paired with plate heat exchangers, these boilers can supply both sanitary hot water and space heating simultaneously.
-
Industrial Processes: Ideal for food processing, chemical plants, and textile finishing where stable, corrosion-free hot water is essential.
Modular configurations allow multi-circuit operation, supplying various temperature zones without mixing or cross-contamination—an advantage for complex facilities or multi-tenant buildings.
Conclusion
By harnessing the physics of phase change under vacuum, vacuum hot water boilers deliver a compelling mix of safety, efficiency, and longevity. Their ability to boil and condense water at reduced temperatures not only cuts fuel use but also slashes maintenance costs. For any application demanding reliable heat with minimal environmental impact, vacuum boilers represent a forward-looking choice in thermal technology.